Tire aquaplaning. Rubber processing. Tire noise.
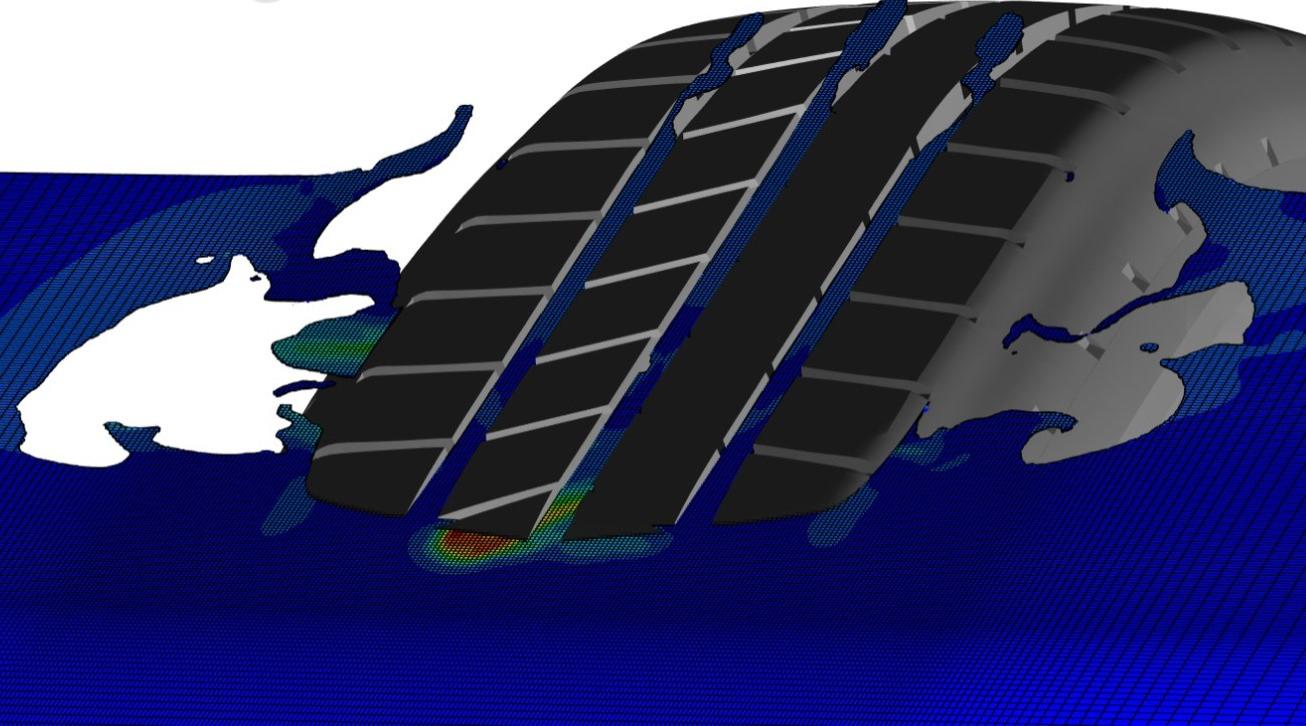
Tire and rubber industry has always been facing various technical challenges and pioneering numerous state of the art technologies in regards to engineering design, manufacturing, application and as well the engineering simulations. As Capvidia, accepting the challenges of tire simulations, our development and project application teams have always put a strong emphasis on the different aspects of tire simulations. Through this emphasis FlowVision has been being constantly improved and validated, responding the industry needs.
Today, we proudly observe that FlowVision is an irreplaceable CFD tool for those who focus on the most challenging simulations in tire industry including aquaplaning, rubber processing, and finally the aeroacoustics.
Aquaplaning
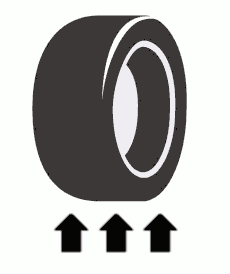
Aquaplaning (hydroplaning) is a phenomenon resulting mainly in loss of traction and since the physical mechanism is based on water film presence between the tire and the road surface; it inherently turns out to be an interdisciplinary expertise area of fluid and structural engineering supported by simulations.
FlowVision’s unique FSI integration with Abaqus allows for simulating 2-phase flow around rotating and elastic tire bodies, tackling the technical challenges included, hence providing realistic simulation results. In such cases, the effectiveness of tire tread patterns is compared to reduce the risk of hydroplaning and increase skid-resistance.
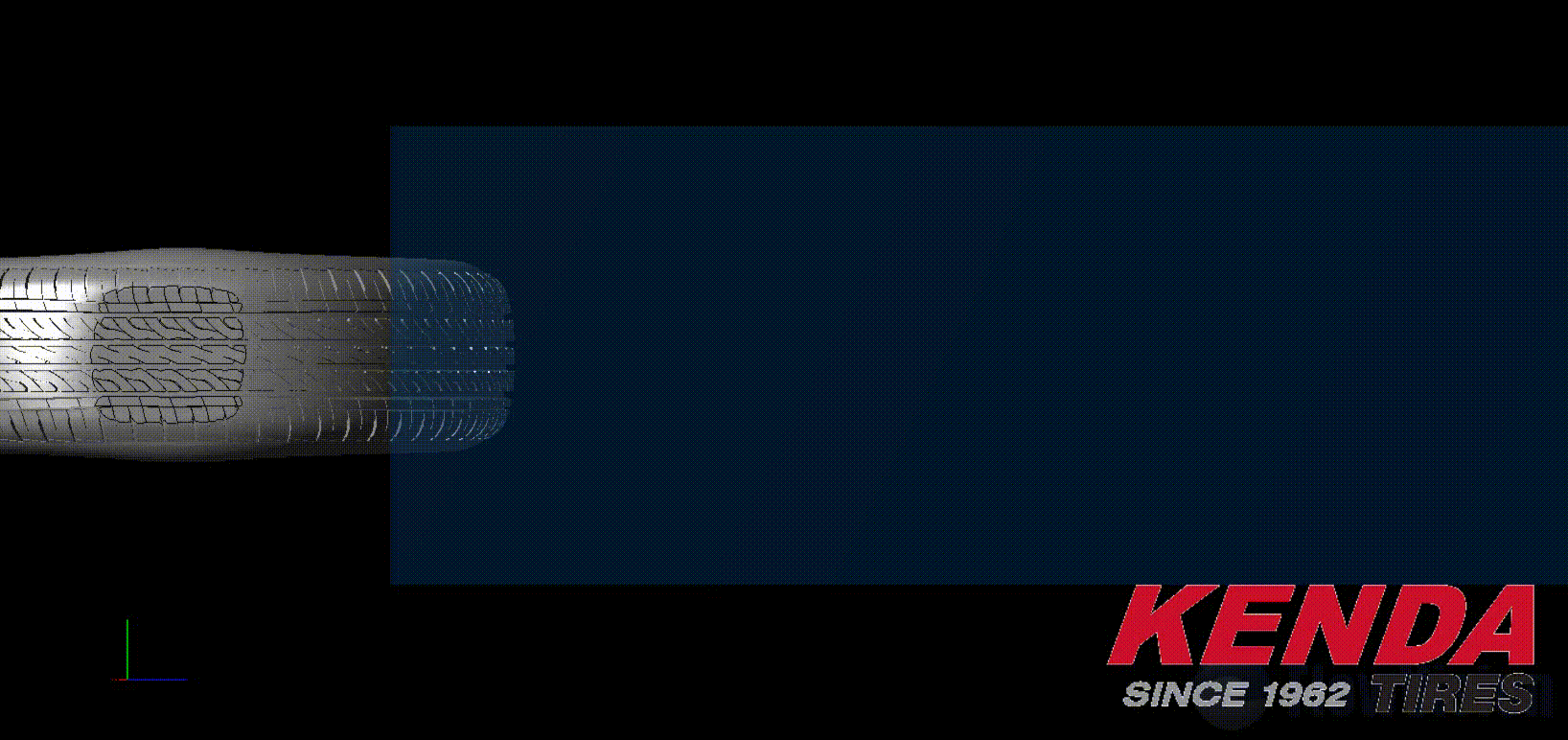
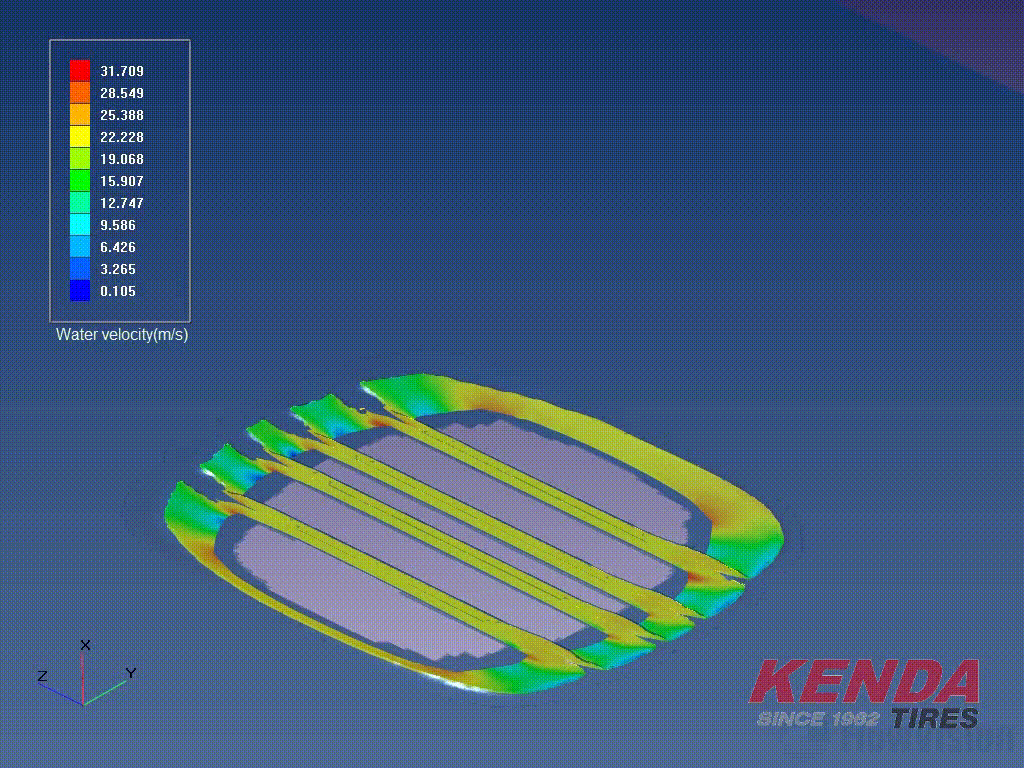
Why Abaqus – FlowVision FSI solution?
- SGGR – Sub Grid Geometry Resolution
- Work with actual geometry, not approximated topologies
- Conservation of mass, no water leakage or loss
- FSI Coupling
- No need for 3rd party software, such as MpCCI
- User-friendly FlowVision MPM & workflow
- Direct matching of FE & CFD
- Independent time stepping algorithm
- User Experience
- High-end technical support experienced on aquaplaning
- Shorter lead times
- one full simulation overnight
- with regular workstations
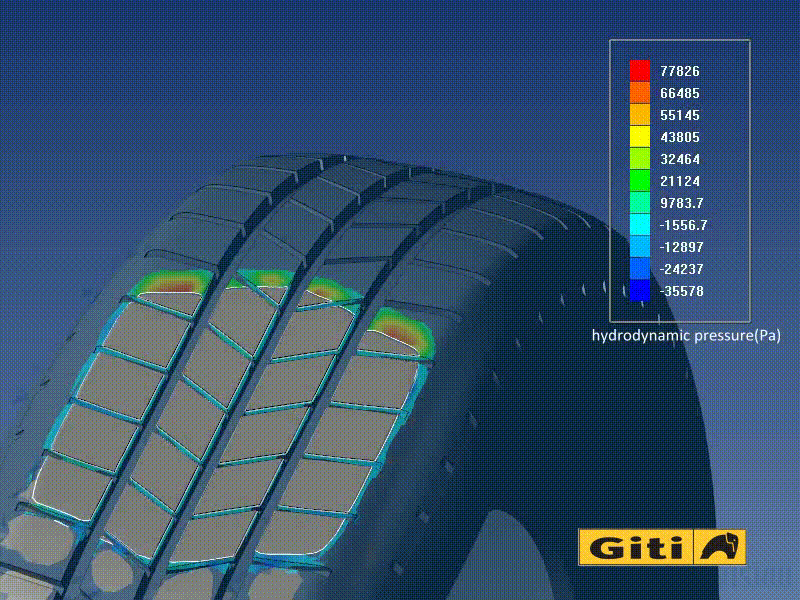
Rubber processing
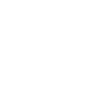
The facts that about three-quarters of natural latex being used for tires and more than half weight of a tire being composed of natural and synthetic rubbers; clearly indicate the significance of rubber processing for tire designers and manufacturers. Where rubber processing consists of four basic steps; mastication, mixing, shaping, and curing; here at Capvidia in close collaboration globally with our users; we have already covered the modeling of the all three steps which are subject to engineering simulations; rubber mixing, rubber shaping with either extrusion or molding, and finally curing which is mostly the vulcanization process.
In order to obtain a reliable simulation framework for rubber processing; various physical phenomena are modeled including but not limited to the rheology and non-Newtonian fluids, physical mixing by means of complex dynamic mechanisms, and chemical reactions. Being aware of these requirements; FlowVision CFD software package, being further enhanced for specific means such as an embedded mathematical representation of vulcanization, has been positioned as a ready-to-use tool for accurate engineering simulations in the area of rubber processing.
Physical modeling phenomena
- Advanced VOF Method
- Non-Newtonian Flow
- Power Law Model
- Bird-Carreau Model
- Herschel-Bulkley Model
- Non-Isothermal Flow
- Viscosity as a Function of Temperature
- Moving Bodies
- Rotating Mixer Rotors
- Translating Mold
- Implemented Formulas with Using Formula Editor
- Prediction of Die Swell
- Calculation of Viscous Dissipation
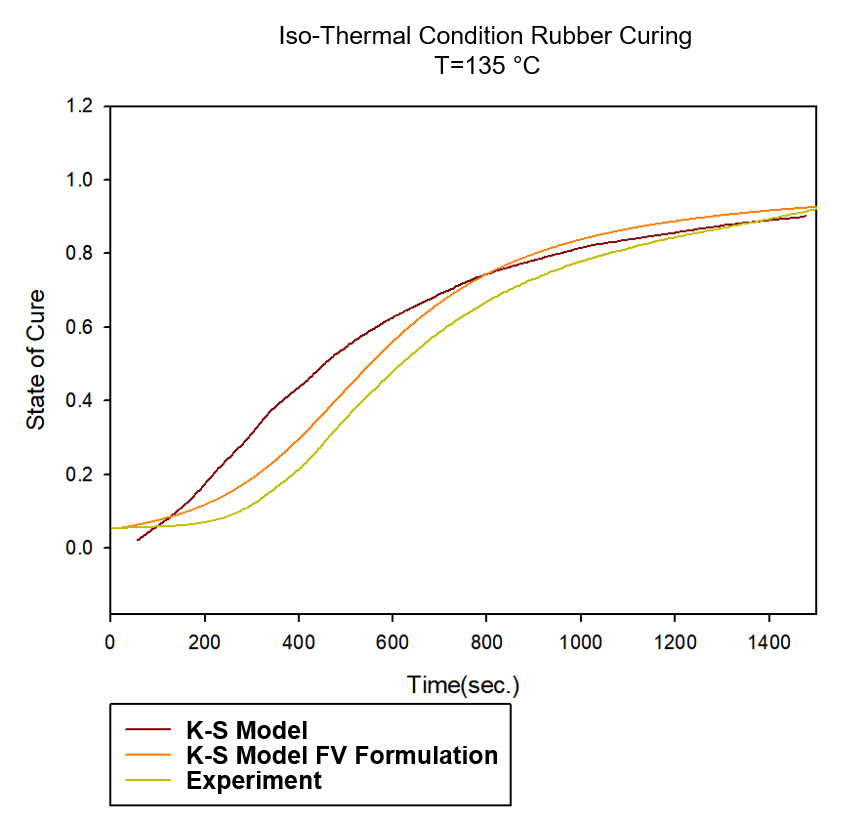
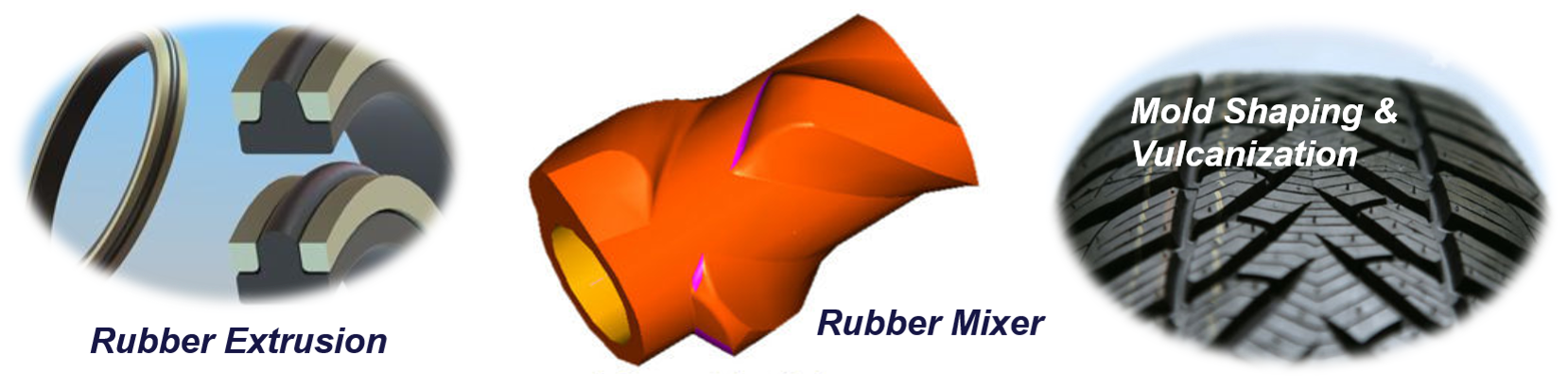
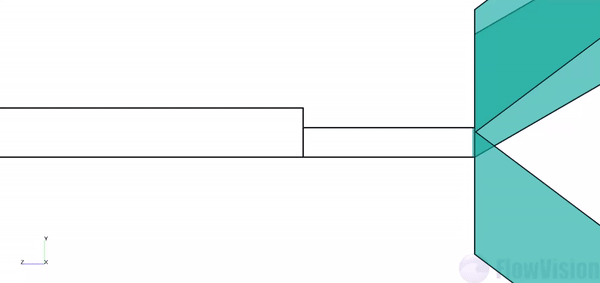
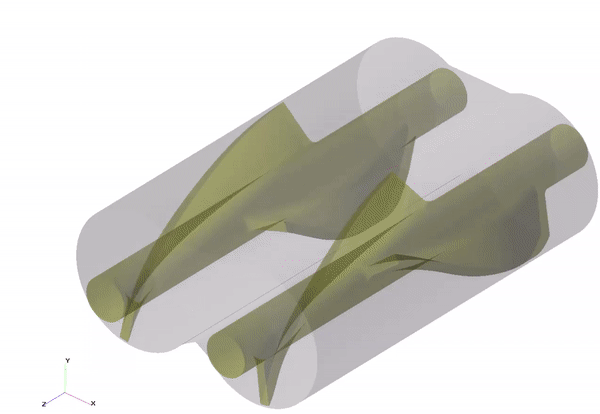
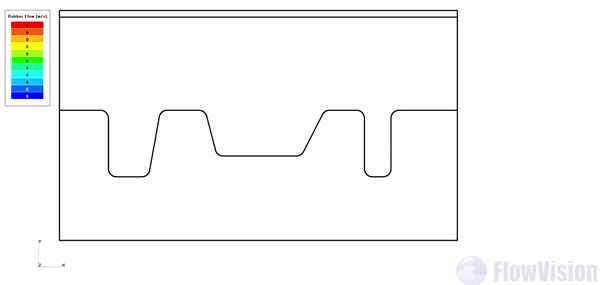
Tire noise
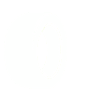
In modern automobiles, prevention of excessive tire noise is one of the key expectations and listed as one of the tire ratings regulated in most of the globe. Accompanied with emerging acoustics and coupled aeroacoustics simulations, today, the tire design workflows start to rely more and more on engineering simulations to ensure that the final products are conforming to the aforementioned regulations.
In this area, coupling FlowVision CFD software with Abaqus FEA and/or LMS Virtual.Lab, provides a well-structured computational aeroacoustics approach, incorporating a smooth workflow and intuitive user experience. Furthermore, this approach is established on the base of critical software and coupling technologies, playing vital roles to overcome the challenges of high fidelity representation of actual geometry and physics which are crucial for a reliable tire noise prediction by engineering simulation means.
Tire noise
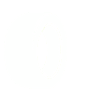
In modern automobiles, prevention of excessive tire noise is one of the key expectations and listed as one of the tire ratings regulated in most of the globe. Accompanied with emerging acoustics and coupled aeroacoustics simulations, today, the tire design workflows start to rely more and more on engineering simulations to ensure that the final products are conforming to the aforementioned regulations.
In this area, coupling FlowVision CFD software with Abaqus FEA and/or LMS Virtual.Lab, provides a well-structured computational aeroacoustics approach, incorporating a smooth workflow and intuitive user experience. Furthermore, this approach is established on the base of critical software and coupling technologies, playing vital roles to overcome the challenges of high fidelity representation of actual geometry and physics which are crucial for a reliable tire noise prediction by engineering simulation means.
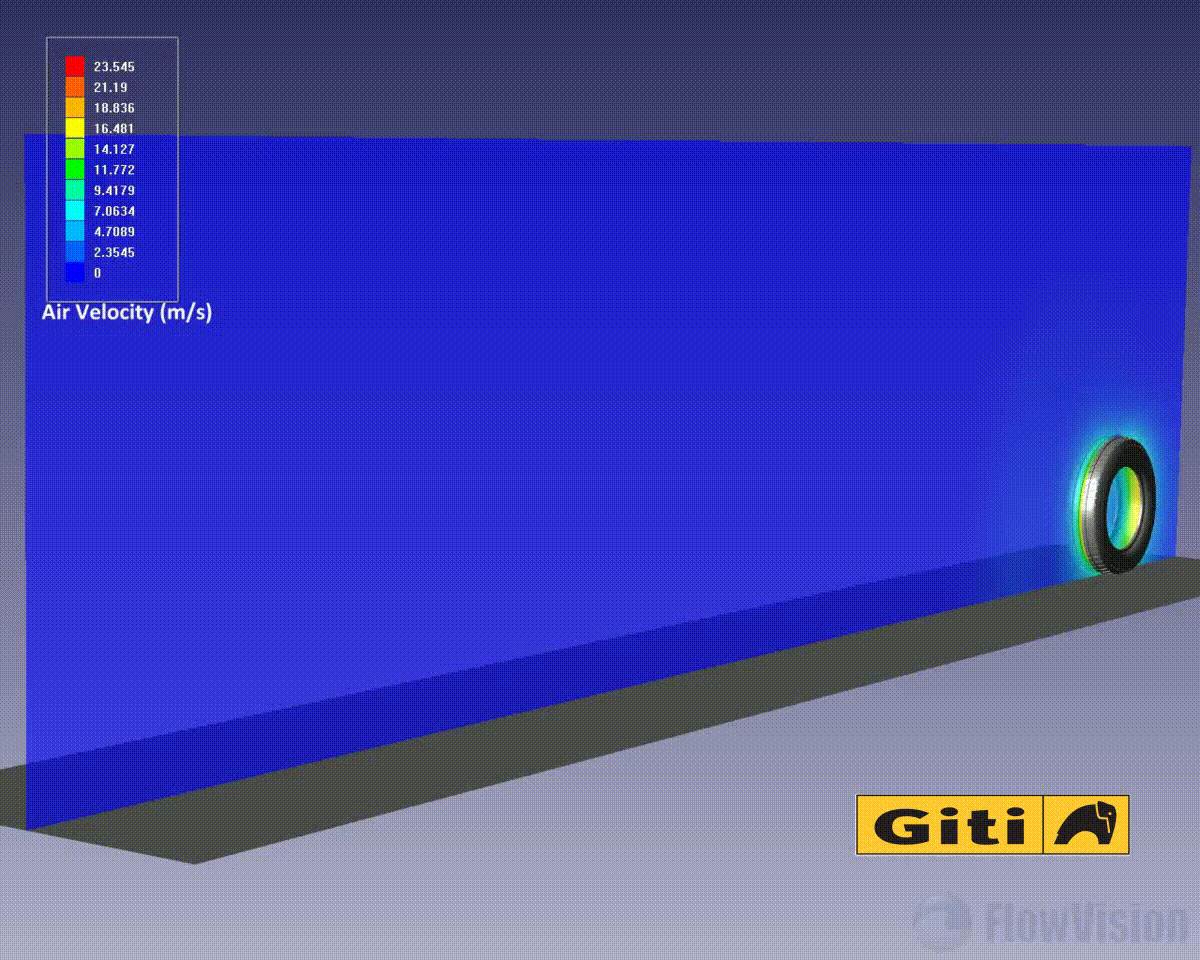
Challenges related to high fidelity representation of actual geometry & physics
Narrow & complex groove geometries
Elastic solid materials -> large deformations -> significant changes in fluid volumes
Rotating and translating tire bodies
Contact surfaces between tire and road
Coupling between CFD – FEA – Acoustics solvers
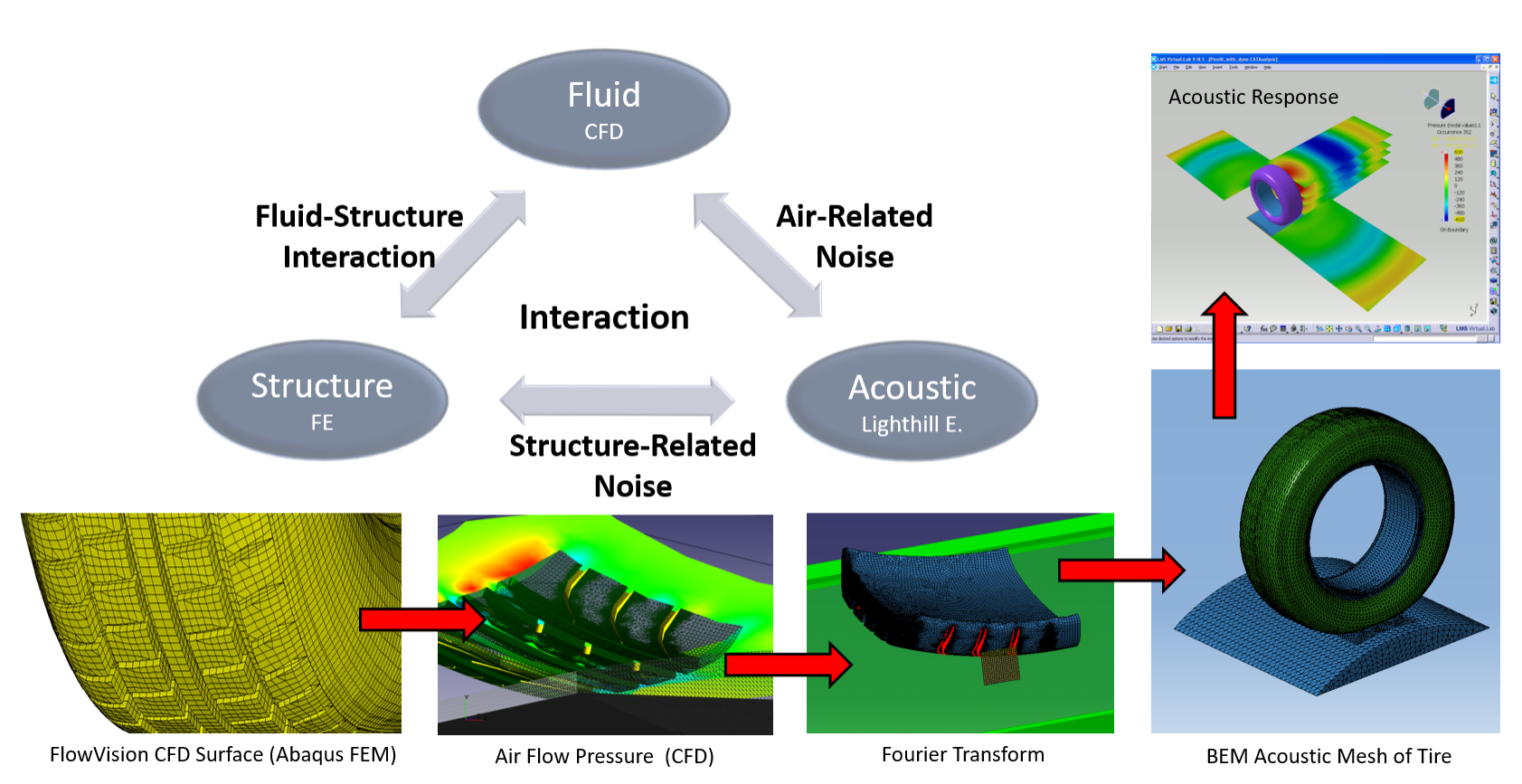